To realize your ideal heating process
IH (Induction Heating) is... ;
1. Clean heating
2. Pinpoint heating
3. Non-contact heating
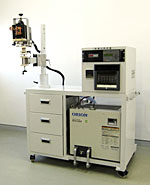
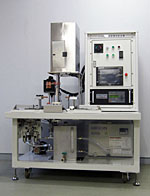
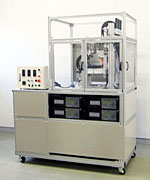
Alonics designs and manufactures IH system to realize customers' ideal processes such as brazing, soldering, shrinkfitting, and annealing using the wealth of knowledge and experience we have accumulated over many years in the field of high frequency and our expertise in many industries.
When we develop system, we listen to the customer's ideal processing in detail and propose content suitable for the requirements.
Product SampleMovie "Induction Heating System for Beginners"
Why we recommend IH
IH offers various advantages over other heating methods.
Heating methods | Concerns | Advantages of IH |
---|---|---|
Flame | CO2 emissions | Since no flame is used, it contributes to decarbonization (carbon neutral) efforts. |
High temperatures affect the work environment | Minimal impact on the work environment due to heating only the necessary portion and time | |
Temperature control is difficult | Temperature measurement feedback allows fast control of output | |
Requires skill to work | Easy controllability prevents operator variability | |
Furnace | Large footprint | Small footprint. Power supply and heating coil can be installed far apart for effective use of space |
Temperature rise takes time. | Heats up immediately with a steep start-up (5 ms) after power-on | |
Resistance heating | Difficult to reproduce | Excellent reproducibility with stable output |
System configuration
IH system is not efficient even if only the power supply is considered.
The Balance and quick response of the power supply (generator), heating coil, and control device maximize the functionality of the system.
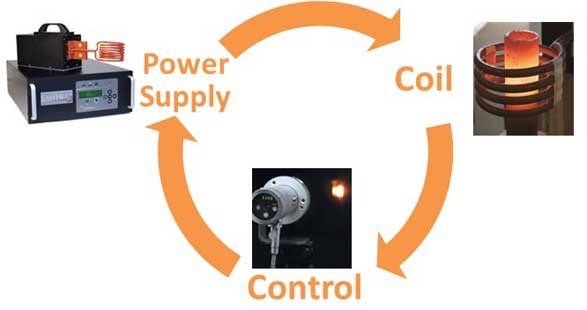
1. Power Supply (Inverter)
The core of an induction heating system is the power supply (Inverter).
An induction heating power supply generates a magnetic field around the heated object (work piece) by sending an alternating current through the heating coil.
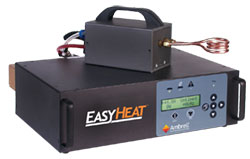
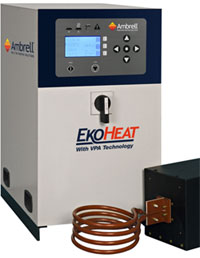
The output and frequency of the power supply differ depending on the heating process required for the object to be heated (workpiece), such as the heating range and heating temperature.
IH power supply (Inverter)Related device
Remote workhead
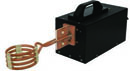
It is a matching device that efficiently sends power to the heating coil. By installing it away from the power supply, you can use the workspace effectively.
Cooling system
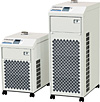
Water-cooled systems require a heat exchange mechanism to remove the heat generated by the system. ORION chillers, with their reliability and proven track record, are the best choice.
2. Heating coil

The AC current from the power supply generates Joule heat, which causes the metal in the coil to self-heat.
The key to an efficient process is an appropriate shape (round, helical, pancake-shaped, etc.) that matches the material of the work piece to be heated and the size of the area to be heated.
Related device
Heating furnace
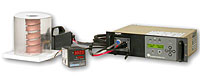
Easy-to-handle furnaces are available for applications such as curing, brazing, soldering, melting, and drying.
3. Control device
Control by temperature
Accurate temperature measurement through a radiation thermometer (Infrared Pyrometer), temperature controller, and instantaneous response allows for faster control of the power supply output and more precise processes.
Control via RS-485
Acquire process data, change settings, and send profiles.
eVIEW induction heating software
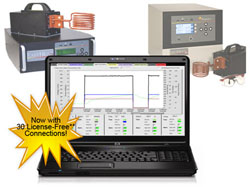
Visualize, analyze, and store process data from induction heating systems in real time.
You will get the best IH solution
We can provide the best solution for your needs by selecting and designing the appropriate model for each devices, and by optimizing the design by combining each device in a well-balanced and effective manner.
In addition, the compact configuration of the system allows for easy integration into production lines.
We can even design and manufacture equipment for integration into production lines, so please feel free to contact us for more reliable and efficient production and research.