Brazing is Ideal for Many Applications in Manufacturing
Brazing is a process for joining two metals with a filler material that melts, flows and wets the metals’ surfaces at a temperature that is lower than the melting temperature of the two metals.
Protection from oxidation of the metal surface and filler material during the joining process is achieved using a covering gas or a flux material.
Brazing and silver soldering are terms that usually refer to the joining process where the filler materials have a melt temperature above 400°C (752°F) to create a stronger joint.
Video: IH brazing application examples
Advantages of IH
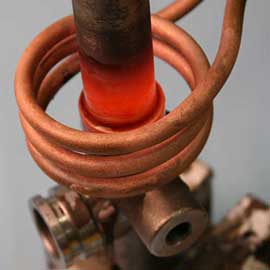
Conventional brazing process: Torch
Torch brazing is the most common form of brazing today, but requires a skilled operator. However many manufacturers are finding it harder to recruit experienced brazing operators and the open flame raises regulatory and safety concerns for manufacturing plants.
Conventional brazing process: Furnace
Furnace brazing is another widely used technique. Manufacturing companies today are looking to improve production efficiency, reduce manufacturing costs and replace energy and space inefficient furnaces while improving product quality.
IH brazing offers numerous benefits
IH brazing addresses the issues of torch and furnace brazing by removing the requirement for a skilled operator, by reducing energy costs and by decreasing the equipment footprint while implementing a lean manufacturing process for higher quality parts.
- Throughput: induction generates heat only in the portion of the part needed
- Repeatability: after the coil and heating process are defined, you can count on a precise,
consistent quality braze every time - Easy integration: into a lean manufacturing process
- Safety: no open flame or hot furnace
- Small footprint: frees up valuable factory floor space
IH automatic brazing system
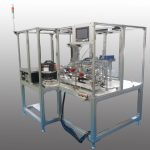
Alonics's [IH automatic brazing system] is an easy-to-operate automatic machine that takes advantage of induction heating.
It is easy and safe to operate by simply setting the workpiece in the loading slot and turning on the switch, and automatically processes everything from flux coating to brazing.
IH brazing process
IH brazing is used in the joining of many different metals for multiple applications. Typical joints are steel-to-steel, steel-to-brass, steel-to-copper, copper-to-copper, aluminum-to-aluminum and copper-to-aluminum
Aluminum Brazing Applications
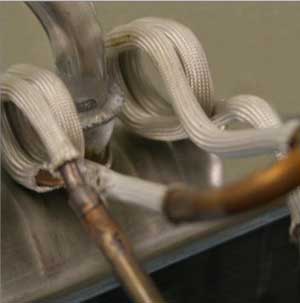
Aluminum requires a lot of energy to heat using induction and its thermal conductivity is 60% compared to copper.
Coil design and time for the heat to flow is critical in a successful IH brazing process for aluminum parts. Recent advances in lower temperature aluminum braze materials has allowed induction to effectively replace flame and furnace heating in brazing of aluminum assemblies.
The low melt temperature of aluminum requires that the IH brazing process apply the energy to the part correctly to raise both part surfaces to the braze flow temperature at the same time without overheating and melting the edges of the part.
Get the experience you need for aluminum brazing applications with Alonics.
Steel Brazing Applications
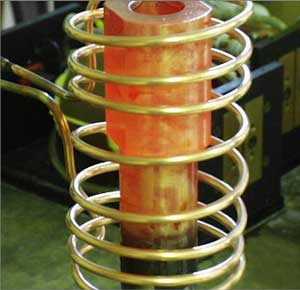
IH brazing is the ideal technique for joining steel parts where welding is not suitable.
A well-designed induction brazed steel joint provides many benefits including part geometry integrity and lower part stress.
Carbon and stainless steel have high resistivity – they couple well to induction energy and heat easily. However, they have poor thermal conductivity so the induction brazing of steel parts should not be rushed. With steel, it is important the heat is given time to soak through to the joint surface for proper flow and wetting out of the braze material.
Copper-based alloys are often used as a low-cost braze material on carbon steels while nickel based alloys are used for stainless steels.
Steel, Copper and Brass Brazing
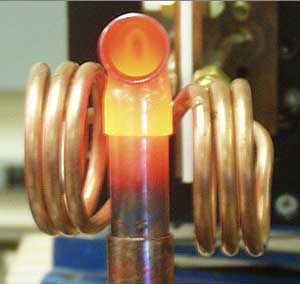
IH brazing is an excellent method of joining parts made of dissimilar metals.
Applications with mixed metal joining include steel-to-copper, steel-to-brass and brass-to-copper. With these materials, it’s all about timing.
For a successful brazed joint between different metals it is critical that both metal surfaces reach the braze flow temperature at the same time as the joint.
The induction heating solution must take into account the different thermal conductivities of the materials, and the time each material takes to get to temperature.
IH systems for brazing
With our EASYHEAT and EKOHEAT, we offer a wide power and frequency range with our induction heating systems.
Whether you’re brazing large or small parts or multiple metal materials, Alonics can help you maximize cost efficiencies and productivity. Our systems are versatile with multiple capacitor and tap transformer configurations.
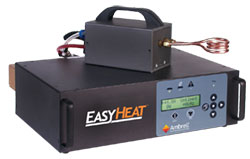
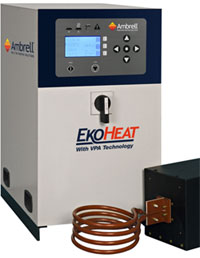