Rapid heating makes a high-volume process
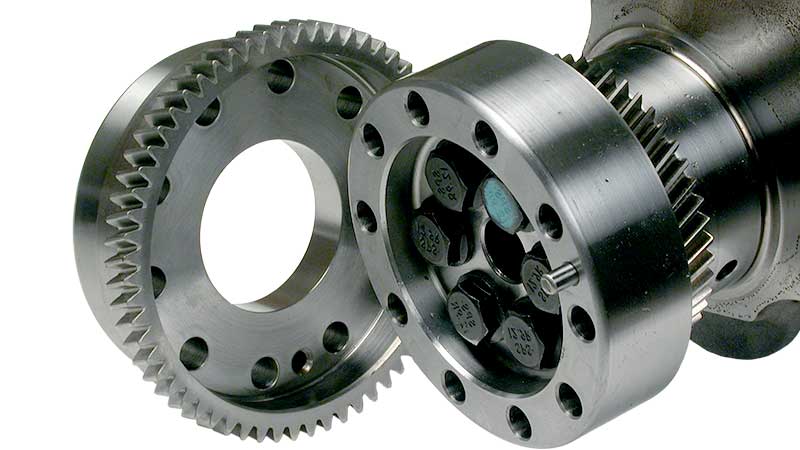
Shrink fitting is a process where a size change after assembly, which can be achieved with induction heating, creates an interference fit. By heating or cooling one component prior to assembly and allowing it to return to the ambient temperature after assembly, the thermal expansion creates a joint. In fact, after the assembly cools, it generally cannot be separated without reheating the assembly to reverse the process.
Video: IH shrink fitting application examples
Shrink fitting process
Typically, with shrink fitting you heat a part to roughly 150 to 300 ˚C (300 to 500 ˚F), which is enough to allow the part to expand enough to enable insertion without changing the metallurgical structure
Common problems
- The accuracy of the inner diameter of the housing and the outer diameter of the shaft is poor, and it does not fit after cooling
- Shaft does not fit in correct position due to lack of alignment during insertion
- Joint surfaces become dirty
Tips for good shrink fitting
- If you heat it enough for a long time, the temperature will be even and the expansion will be sufficient.
- Use an alignment jig to ensure a smooth drop into the housing
Advantages of IH
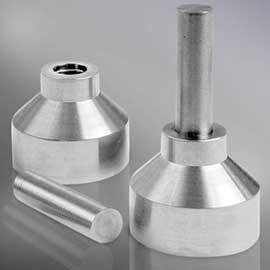
- Precise heating: Localized heating means heat is directed only where it is needed, not to the whole part, minimizing distortion.
- Rapid heating: This makes induction a great fit in a high-volume shrink fitting production process.
- Repeatability: With induction, you can expect the same result every time. So once the process is determined, it is set and can be repeated over and over. This also makes it highly conducive to automated manufacturing processes.
- Flameless heating: Which offers safety advantages and introduces less heat into the work environment.