Floats metal in the air and melts it
Levitation melting is known as a method to minimize contamination during dissolution of conductive materials such as metals.
Once the material has melted, the induction power is shut off, and the molten mass can be dropped or forced into a mold for forming. This application is applied in the jewelry, dental, electronics, and aerospace research industries for a contaminant-free environment.
Applications where levitation melting is useful include jewelry, dental materials, electronics, and aerospace research.
Video: levitation melting application examples
Advantages of IH
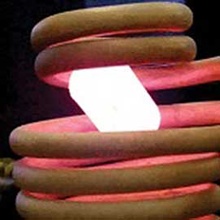
IH is capable of heating very small ranges precisely within manufacturing tolerances without compromising their respective metallurgical properties.
Levitation melting relies on a complex force balance in three dimensions to melt, while the power supply's precise automatic frequency tuning and power control achieves consistent, reliable/reproducible melting.
Principle of levitation melting
When a conductive material is placed in an induced magnetic field, an induced current will flow in it, which will generate heat due to the resistance of the material.
During heat generation, the current flowing through the material creates a magnetic flux opposite to that generated by the current flowing through the coil, and that force acts on the molten material.
By properly controlling this force, it is possible to levitate the dissolved material.
As a first step, a helical cone-shaped induction coil is used to generate a strong magnetic field gradient.
Next, a coil wound in the opposite direction is built on top of the conical coil as a backing plate to provide vertical stability.
The combination of the conical coil and backing plate creates a "null(zero)" zone where the molten metal stays.
When RF power is continuously applied, the metal melts and remains suspended.
In this floating zone, the metal is not contaminated by impurities and is not subject to mechanical interference.