Compact system configuration
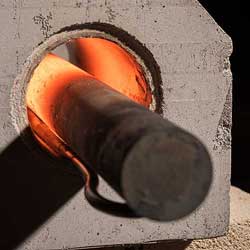
Forging, the oldest means of metalworking, involves using hammers to deform metal to increase its strength.
In most cases, the heat forming process raises the temperature of the metal in an oven.
Applying heat means deforming at a temperature higher than the recrystallization temperature.
This process requires uniform heating.
Conventional gas furnaces or flame processing are inefficient in terms of both energy and time.
However, IH makes it possible to achieve rapid and accurate heating of only the workpiece.
It can also be used for high-speed, high-volume forging processes by placing the remote workstation directly in the forging process production line.
Video: IH forging application examples
Advantages of IH
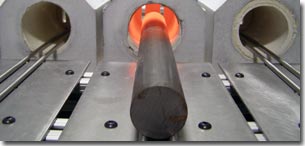
- Small footprint: IH systems are modestly sized compared to ovens
- Energy savings: energy is supplied only to the workpiece, minimizing waste heat
- Increases production rates with faster heating cycles
- Reduces defect rates with repeatable, reliable heat
- Eliminates variability from operator-to-operator