Fast and stable process
The process of induction hardening is most commonly used in steel alloys. This is because there are many mechanical parts, including gears, shafts, and springs, that are subjected to surface treatments prior to delivery in order to enhance what is known as wear behavior. However, it's important to keep in mind that the level of effectiveness of any given induction hardening treatment depends on a variety of factors, including the modification of surface material properties and the introduction of residual stress. But above all, the process is known to be one of the most effective and widely employed processes meant to increase component durability.
Hardening is ideal for a wide variety of applications in the transportation, aerospace, and energy industries.
There are generally two methods of hardening;
- Through hardening
- Through hardening treats the entire part and is used on medium and high carbon steels for moderate strength and surface hardness.
- Case hardening
- Case hardening treats the part’s surface area and some of the interior area, according to the depth of hardening requirements of the application.
Video: IH Hardening application examples
Advantages of IH
IH concentrates heat precisely where it is needed and provides the necessary control.
Single Shot Hardening
IH technology, applied in a single shot approach, allows the portions of the part that require hardening to be heated simultaneously – followed by quenching.
Ideal for flat-face hardening or edge hardening, IH delivers faster production times compared to other hardening methods. And, induction heating coils allow the creation of longitudinal current flow in the part – for effective hardening of geometrically complex components.
Tooth by Tooth Hardening
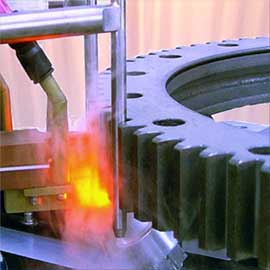
IH hardening allows precise and selective treatment of the tips of gear teeth, to provide enhanced hardness and increase the gear’s durability and resistance to wear – without altering the metallurgy of areas of the part that do not require treatment.
Tips for good hardening
The effect of quenching on the result is governed by how it is cooled.
The quenching refers to the rapid cooling of a metal piece or workpiece in either water, air, or oil in order to bring about specific qualities. The cooling rates are improved by increasing their flow rate.