No cleaning process required
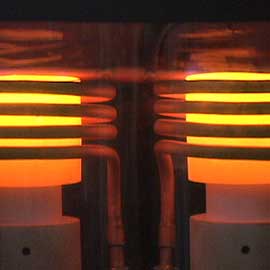
Brazing in controlled atmospheres (vacuum or inert gas) significantly improves its quality and does not require costly cleaning processes.
Heating by a flame in a normal oxygen containing atmosphere can cause oxidation, scaling and carbon build-up in the workpiece.
To clean them, it is necessary to use fluxes or expensive acid cleaning baths.
Depending on the type of parts and brazing material, it may be necessary to work in an atmosphere (inert gas such as argon or vacuum).
Brazing in inert gas is used for nickel, titanium, superalloys, stainless steel, refractories, etc.
Depending on the type of part and material to be brazed, it may be necessary to work in an atmosphere (inert gas such as argon or vacuum).
Brazing in inert gas (brazing) is used with nickel, titanium, superalloy, stainless steel, refractory materials, etc.
Advantages of IH
Conventional batch-type vacuum furnace brazing requires a large equipment size and has limitations in terms of quality control.
IH, in which the workpiece itself is directly heated, is an extremely effective means of achieving controlled heating with high reproducibility even in an atmosphere (vacuum or inert gas).
In addition, the compact device configuration and easy to operate.