For hot bending and weld stress relieving
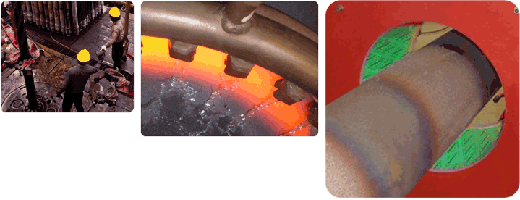
Whether you are involved in hot bending, weld stress relieving, heat treating, coating or brazing, induction heating may be the ideal approach for your operation.
IH applications for tube and pipe
Induction heating is the preferred solution for tube and pipe manufacturers looking for more effective, cost-efficient heating technology.
Tube and Pipe Coating Curing
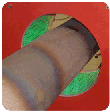
IH system are fast, efficient choices for all stages of the curing operation.
In preparation for coating, induction heating is used to remove surface moisture from pipes, preheating the pipe to the correct temperature for coating.
In addition to requiring less floor space than traditional furnaces and ovens, induction systems offer ergonomic benefits, are environmentally friendly, and have the unique capacity to selectively heat only portions of a tubular product.
Pre- and Post-Weld Heating
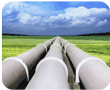
With the use of more thin-wall steel alloy pipes in today’s oil and gas pipelines, manufacturers and installers are turning to the fast, accurate and uniform heating of IH systems.
Traditional gas flame and resistance heating systems are often impractical when these higher temperatures are required. Not only are they too slow to meet the cycle times demanded by the industry, but also the heating can be inaccurate and can lack uniformity around the full circumference and bandwidth of the weld joint.
Hot Pipe Bending
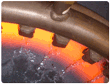
Induction heating is the preferred heating method for bending of larger thicker walled pipes. This is due to the focused narrow band heating offered by the induction process with the resulting higher quality bends with lower ovality and wall thinning than other bending methods.
Because of this quality and accuracy, induction hot pipe bending is the preferred alternative to traditional fit-and-weld procedures, and can help companies meet the rigorous safety demands of the chemical and energy industries.
Drill Pipe Heat Treatment
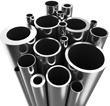
Drill pipe ends are thickened by heating the pipe end to 1100 °C (2012 °F) before forging. Induction is often used to heat multiple pipes in a single channel coil, or sequentially in a multi-position coil that produces one pipe-end every 150 seconds. These heating methods provide the time required for the heat to travel through the pipe wall, yet meet the 180 seconds floor-to-floor cycle time.
Brazing Diamond or Carbide Inserts onto Oil and Gas Well Drill Bits
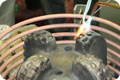
In drill bit manufacturing operations, multiple tool inserts (typically between 40 and 60) are individually brazed onto a single drill bit. These inserts may be a polycrystalline diamond compact (PDC) or tungsten carbide inserts (TCI).
Induction heating is an excellent technique for pre-heating the drill bit to 600 °C (1100 °F) in preparation for the torch brazing of the diamond inserts.