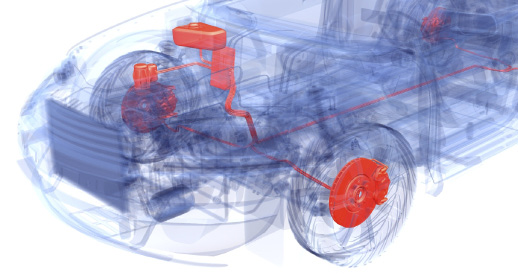
Protective coatings used on automotive brake rotors provide a more durable and visually appealing product by reducing rust and corrosion. Once protective coatings are applied, typically they are dried or cured in an oven. However, using induction heating for rotor finishing saves on energy costs and valuable production time.
Advantage of IH
IH generates the heat from within the rotor improving the quality of the finished coating by curing from the metal coating interface allowing for any outgassing during the curing process. This flameless, concentrated energy, saves the wasted time and energy in ramping up an oven as well as saves ambient heat surrounding the part.
- Provides the correct temperature across the rotor
- Each rotor has the same cure process
- Safe and effective: a flame-less concentrated heat energy
- Flexible: coils can be configured to any rotor size
- Energy savings: no furnace to ramp up
- Production savings: faster part throughput
- Easily integrated into existing manufacturing lines
The Cure for Brake Rotor Coatings
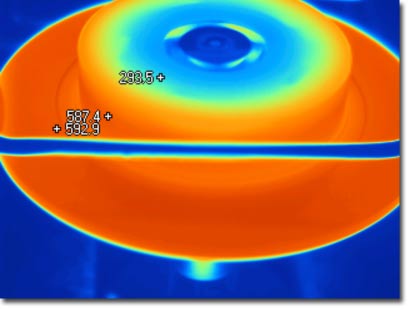
Thermal images (above) shows the even temperatures on the rotor surface while keeping the center hub cool.