Fast, consistent, pinpoint heating
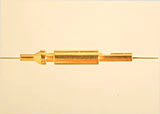
Fiber optic cable manufacturers are looking for faster, more consistent, and more precise heat sources for soldering, hermetic sealing, epoxy curing, fiber pull-out, and other heating processes.
Fast heating times and temperatures below 260°C (500°F) are desired for soldering optical fibers, which are sensitive to heat.
However, commonly used heating methods, resistance heating and hot air, are challenging, and automation for high-speed production is not easy.
Advantages of IH
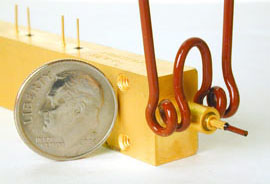
With proper coil design, induction heating can heat small areas with pinpoint accuracy.
Heating cycles can be reduced to as little as a few seconds, depending on the application.
Induction heating is a clean heating method for hermetic sealing because there is no hot air containing impurities and the heating coil does not touch the part directly.
And you can automate the entire process with maximum speed and consistency.
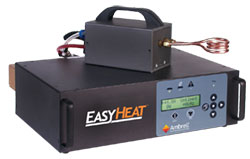
Utilizing an induction heating power supply with advanced solid-state technology, the IH system is capable of ±1.1°C (2°F) temperature control, making it adaptable to all types of solder.
Even the compact size of the EASYHEAT is sufficient for quick heating of small parts at temperatures below 260°C (500°F).