For fast and accurate maintain engineering
In the aerospace industry, engine components are expensive, so repairing them rather than replacing them has become much more economical.
Batch-type vacuum furnace brazing has traditionally been used to apply heat in this repair, but induction heating can be used in a variety of situations.
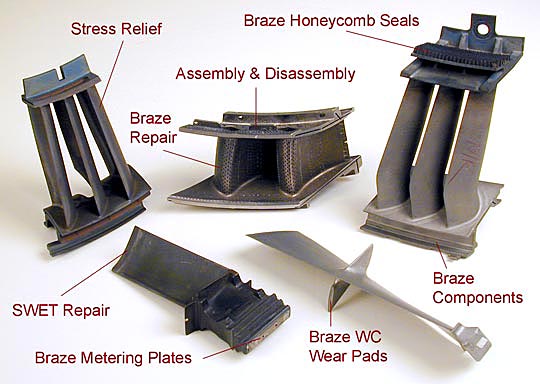
Advantages of IH
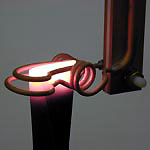
Utilizing IH power supplies (invertor) with advanced solid-state technology, IH system offers many advantages for heating in a controlled atmosphere.
Compared to batch-type vacuum furnaces, they provide precise, contactless heating in a compact, cost-effective package. This provides fast, accurate, and consistent manufacturing and repair processes.
IH applications in the aerospace industry
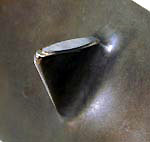
In many heat-using processes such as brazing, soldering, and preheating, IH offers high quality heat treatment with no variation in reliability and reproducibility.
Rapid and energy-efficient IH is very effective in repair work that requires quick response.
Application | Working point | Heating Temp. / Sec. |
---|---|---|
Welding | Turbine engine fan blades | 982°C in 5 min. |
Heating | Inconel billet | 1121°C in 12 sec. |
Heating (Melting and expulsion wax from the inside) | Titanium blade | 260°C in 4 min. |
Preheating for hot molding | Titanium Rod | 927°C in 60 sec. |
Brazing | Steel Conduit (Ferrule and elbow assembly) | 760°C in 20 sec. |
Soldering | Steel Connectors (Brass block) | 316°C in 20 sec. |
Brazing | Bonding of hydraulic hose assemblies | 1204°C in 7 sec. |
Brazing | Turbine blade (Nickel) | 1093°C in 5 min. |
Brazing | Compressor blade | |
Brazing | Metaling plate for Inconel turbine blades | 1121°C in 5 min. |
Brazing | Honeycomb seal | 1066°C in 90 sec. |
Brazing | Fuel nozzle assembly | 1066°C (1 piece in 3 min.) |
Stress relief | Compressor blade |